浙江精锻机床维修 嘉兴金丰协易冲床维修管理方案
浏览次数:213次
- 产品规格:
- 发货地:上海市嘉定区
关键词
嘉兴金丰协易冲床维修管理方案
详细说明
类型通用配件
动力类型气动
品名冲床维修
可售地全国
加工定制是
是否进口否
特色可上门服务
服务类型维修
使用范围各种冲床
产品名称冲床维修
材质合金钢
适用机床冲床
样品或现货现货
是否标准件是
是否库存是
是否批发是
数量按需定做
冲床的保养和维护?1、保养
A、经常保持中心柱,滑块导柱的干净,以及架模时保持模具底板无脏物,以确保平台的洁净避免划伤。
B、新机在使用1个月时,飞轮处加黄油(包括送料机),如果长时间没有加油,会导致飞轮内部磨损,影响机床的性能,以后每次保养时也需加(耐高温150O以上的黄油)
C、机台循环油的更换:新机在1个月内更换1次,以后每隔半年更换1次,保证机床的正常运行和精密度(32#机械油或美孚1405#)
2、操作安全
A、 不能两人同时操作一台机器,否则会导致机器突然启动,对作业员造成损伤。
B、作业员在手动送料过程中,特别是用手伸入模具里送料时,一定要按紧急停止按钮,以免造成严重的后果。
C、 架模时,要等飞轮完全停止后,方可进行。
3、架模时注意事
A、 不能超过冲床的模高范围(上限和下限内),否则会造成冲床受损。
B、 模具不能打死模,要有0.02~0.04mm的间隙。
C、 架模时①机械锁模型机,固紧冲头滑块后,滑块会下沉0.07~0.15mm
②油压锁模型机,冲头锁紧后,会上浮0.03~0.05mm
D、 模具架好以后,用手摇飞轮一圈,看是否能过模(过模不能太紧
E、若用手动操作时,后一定要放开手动阀(离合器电磁阀上)不然机床主机一经启动,就会开始冲压,对作业员和模具都易造成损伤。
4、定期检查(建议每日检查)
A、油箱内油量是否足够,油是否干净。
B、 三点组合自动喷油器是否有油。(上、下限内)
C、 增压泵浦油量是否足够。(油箱一半以上)
D、有无漏油、漏气现象。
E、 储气桶是否有排水
F、 机台有无异响。
G、保持电控箱内部的清洁、通风顺畅。
5、冲床与的连接
A、 机身和电控箱的插座不能接入过大的负载,在300W以内,否则会损坏机床内部元件。
B、机身侧壁箱上的标有剪刀功能的连接线,当打开剪刀开关时,有220V电压,客户用剪刀功能时需特别注意。
C、送料机、收料机的电源线好不要经过冲床的空气开关和内部其它开关来控制,否则也有过载的危险,以造成严重后果。(其它操作可参照通力高速精密冲床使用说明书)
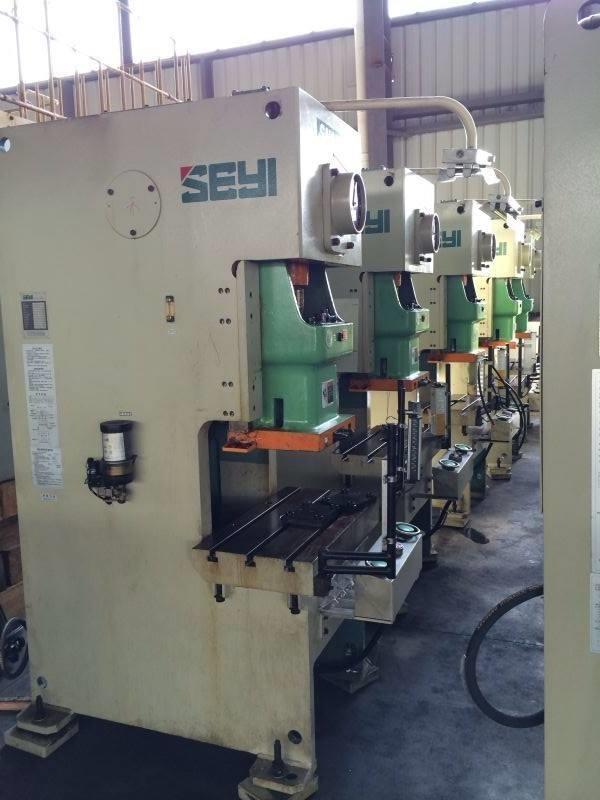
普通冲床就是一台冲压式普通压力机。主要是针对板材的。通过模具,能做出落料,冲孔,成型,拉深,修整,精冲,整形,铆接及挤压件等等,广泛应用于各个领域。冲床的设计原理是将圆周运动转换为直线运动,由主电动机出力,带动飞轮,经离合器带动齿轮、曲轴(或偏心齿轮)、连杆等运转,来达成滑块的直线运动,从主电动机到连杆的运动为圆周运动。
1 、一般冲床曲轴轴承发热 轴套刮的不好,光滑不良 从头刮研铜瓦,查看光滑情况。
2 、从轴承里流出的油里有铜屑 缺乏光滑油,光滑油不清洁 查看光滑情况,拆开轴承进行清洗
3 、导轨烧灼 导轨空隙过小、光滑不良 、接触不良 从头研刮导轨 、调整空隙 、留意光滑
4 、操作时离合器不结合或结合后脱不开 反转健用绷簧失掉弹性键合作过紧 替换绷簧、研刮键的结合空隙
5、离合器脱开时滑块不能停在上死点方位 制动带拉力不够 、制动带过度磨损 、制动轮上有油打滑 调整制动绷簧张力、替换制动器 、用火油洗净制动带及轮周
6 、退料板不作业 打料碰头方位不对 调整碰头方位用手滚动飞轮试退
7、连杆螺丝发作滚动或冲击 锁紧设备松动 旋转锁紧设备
8、连杆螺丝球头在滑块球垫内冲击 球头与球垫压盖接触不良,压盖螺丝松动 刮研球头、球垫、拧紧压盖螺丝
9、按电钮(开)液压冲床不作业 电源断路、热断电器断电、查看一般冲床电路系统消除毛病
连杆和滑块之间需有圆周运动和直线运动的转接点,其设计上大致有两种机构,一种为球型,一种为销型(圆柱型) ,经由这个机构将圆周运动转换成滑块的直线运动。冲床对材料施以压力,使其塑性变形,而得到所要求的形状与精度,因此必须配合一组模具(分上模与下模),将材料置于其间,由机器施加压力,使其变形,加工时施加于材料之力所造成之反作用力,由冲床机械本体所吸收。
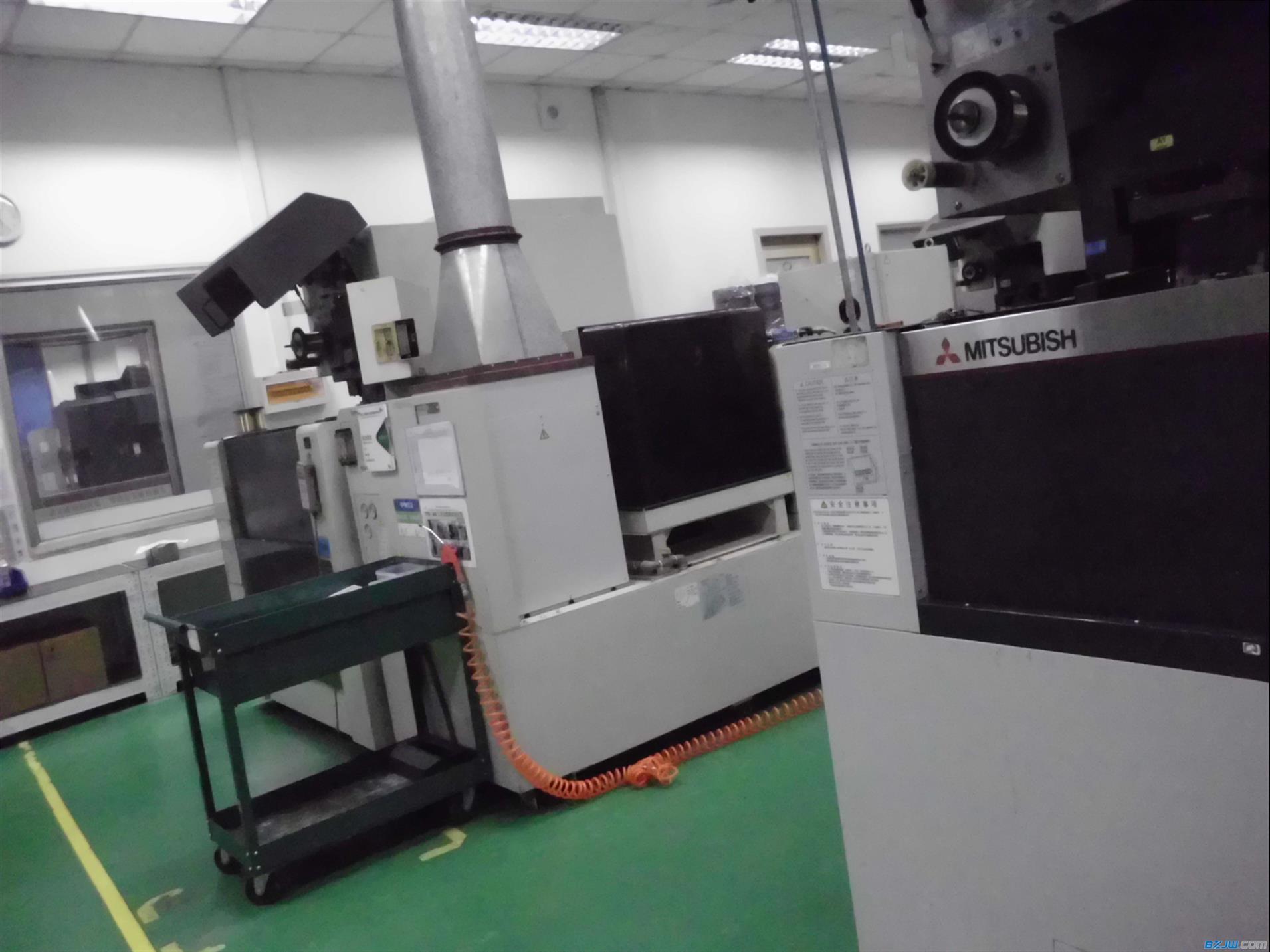
冲床维修知识
1.目的
1.1规范公司普通冲床维修保养程序,确保生产正常进行。
2.适应范围
2.1 适用与公司JH21系列开始固定台压力机(以下简称普冲)的维修保养。
3.职责
3.1 国家注册电工/技工/操作工负责设备的维修保养,操作工负责此设备日常保养式检查,电工/技术负责月/季度/年度维修保养,其当值操作工协助、监督整个维修保养过程。
3.2 生产部负责件的制定和修改;
3.3 此设备的操作工或其班组长负责维修保养后设备的验收;
3.4 生产办公室负责维修保养记录存档,保存期一年。
3.5 所有保养过程中产出的垃圾及废物按废弃物处理程序处理。
4.必要工具及安全事项:
4.1 必要工具:螺丝刀、白布、手套、扳手、警告标牌、兆欧表。
4.2 安全事项:
4.2.1 进行调节、维护、检查等作业,不运转压力机时必须操作如下:
4.2.1.1 按压“紧急停止”按钮;
4.2.2.2 按操纵盒上的电机停止按钮,使电机停止运行;
4.2..2.3 将电源选择开关置于断位,然后抽出钥匙,并交由现场维修保养负责人保管;
4.2.2.4 打开电气箱门,将电源总开关置于断位;
4.2.2.5 将外部断路器上锁;
4.2.2.6 关闭压力机空气管路的截止阀,然后将压力机的残余空气排干净;
4.2.2.7 在操纵盒上挂上写有“警告:正在检查,严禁操作!”的警告标牌。
5.工作程序及步骤:
5.1 日检查、保养:
5.1.1 启动前:
5.1.1.1 检查润滑系统的油泵,并打开油泵向各润滑点供油
5.1.1.2 检查各个油位计中的油面是否达到其割线位置;
5.1.1.3 检查各个压力标的指示值是否在给定的范围内;
5.1.1.4 检查过载保护装置,通气后,气动泵应开始工作,5分钟内应达到额定压力,气动泵停止工作;
5.1.1.5 检查电源指示灯;
5.1.1.6 检查紧急停止按钮:按下按钮能自锁,沿箭头方向转90°时能复位;
5.1.1.7 检查离合器、制动器电磁阀是否失灵。
5.1.2 主电机起动时:
5.1.2.1 检查飞轮运转状态:从压力机后面看,飞轮应顺时针转动,三角皮带不得有震动打滑现象。
5.1.2.2 检查离合器、制动器的操作:“寸动”时,检查曲轴的“寸动”和停止的角度是否过大;
5.1.2.3 检查单次行程:当曲轴转角在160°以前,放开双手运转按钮时,滑块应立即停
止,当曲轴转角转过160°以后,放开双手按钮,滑块应停在上死点;
5.1.2.4 检查紧急停车:运动时。按下“紧急停止”按钮,滑块应立即停止,对“寸动”
以外的操作中滑块未回到上死点时,不能连续运行或单次运行,必须将转换开关
转到“寸动”位置,用“寸动”规范使滑块回到上死点;
5.1.2.5 检查滑块导轨面润滑情况:导轨面应有润滑油脂。
5.1.3 普冲运行期间:
5.1.3.1 检查离合器与制动器:停车时,曲轴应停在上死点(角度指针在-10°——+5°
内);
5.1.3.2检查压力表和转速表是否在规定范围内;
5.1.3.3 检查工作能量:重复若干次工作运转,在满负荷时,滑块行程次数不应减慢。
5.1.4 普冲运转后:
5.1.4.1 目视检查各个部件是否清洁;
5.1.4.2 目视检查每个螺钉有无松动;
5.1.4.3 目视检查气路、油路系统是否渗漏;
5.1.4.4 将储气箱的水分排放
5.1.4.5 将空气过滤器的水分排放。
5.2 月检查/保养:
5.2.1 做好4.2安全事项,确保维修保养过程顺利进行:
5.2.2 清洗空气过滤器;
5.2.3 检查并调整三角皮带张紧度:用手指在三角皮带的施加20N的压力,每一米皮
带约弯曲16mm为合适,否则松开4个锁紧螺栓后,重新调整;
5.2.4 检查凸轮控制器:凸轮板与轴不得有过大的游隙,不得有断续接触,不得有螺栓、
键松动现象,微动开关的滚轮与轴不得有过度磨损;
5.2.5 检查控制继电器:不得有接触不良、响声、运动时卡住等现象;
5.2.6 检查操作按钮和开关:避免灰尘和油污,运动灵活、平稳、定位可靠;
5.2.7 检查离合器与制动器的电磁阀:线圈应紧固,避免窜动;
5.2.8 清理维修保养过程中的垃圾。
5.2.9 做完保养,填写《普通冲床月保养表》,并出电工负责人审查签字后交生产部存档。
5.3 季度检查/保养:
5.3.1 重复5.2的月检查/保养;
5.3.2 将00号锂基润滑脂涂电动式滑块调节链;
5.3.3 更换齿轮箱内的润滑油; 5.3.4 更换连杆处润滑油;
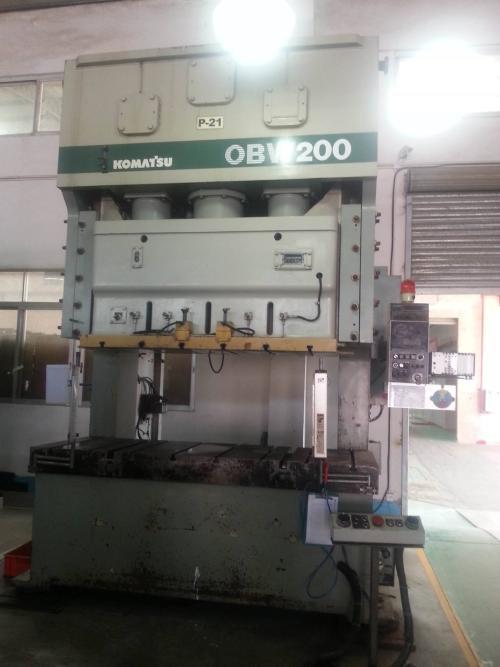
热模锻机床产品特点
本机特性:
1、上下顶料设计,模具型穴斜度减少、原材料消耗量小,节省锻材
2、本机种动能力增高、生产效率大大提高
3、行程快速,锻材与模具接触时间缩短,提高模具使用寿命。
4、突破传统短行程之规格,本机行程增长,更适合各种锻件打拔成型作业。
5、机架两侧作业窗,锻材传送方便,可完成全自动冲压作业。
6、机架高刚性箱形结构,锻件精度高,加工余量减少,适合温热锻造作业,也可以从事冷间锻造。
7、生产效率高,操作简单,维修容易,降低生产成本。
8、传动系统设计,减少噪音污染,符合环保法令。
9、卡模解放设计,复归迅速,操作容易。
10、双层导路设计,抗倾斜率高,容许偏心荷重大,允许多工位锻造,锻件品良。
11、精密集中润滑系统设计,有效减低各摩擦部位效率损失。
12、采用美国吨位数控显示,直观显示实际锻造压力,并且有超负荷控制及报警功能。
13、精度符合标准局CNS检验标准。
m.shccfwz.b2b168.com